Master The Art Of Picking Distilling Equipment For Any Skill Level In 2025
Since ancient times, people have been captivated by the craft of distillation, which has been used to make excellent spirits, extract essential oils, and purify water. The effectiveness, safety, and quality of the finished product are all greatly influenced by the use of the proper equipment during the procedure.
Choosing wisely might be difficult when there are so many options available. The key factors to take into account while choosing distillation equipment for your needs will be outlined in this article.
Understand Your Distilling Goals
Selecting the right distilling equipment starts with identifying your goals. Your purpose, product type, and scale of production play pivotal roles in shaping your decision. Understanding these factors ensures your investment meets your current and future needs. If you're looking to start a distillery, these elements become even more critical to ensure long-term success.
Home Distilling Vs. Commercial Distilling
- Home Distilling: For hobbyists or small-scale users, compact and cost-effective equipment like tabletop pot stills is often sufficient. However, home distillation legality varies widely, so check local laws before starting. Home distilling is commonly used for crafting small batches of spirits, essential oils, or even purifying water.
- Commercial Distilling: Commercial operations demand more robust equipment capable of handling large volumes. Industrial stills, often designed for high capacity and efficiency, must also meet regulatory standards for safety and quality assurance. This category includes specialized stills for whiskey, vodka, gin, and other spirits.
Product-Specific Requirements
- Spirits: Distilling spirits like whiskey, vodka, or rum requires equipment that prioritizes flavor and alcohol concentration. Pot stills are excellent for rich, flavorful products, while column stills are better for high-purity spirits.
- Essential Oils: Steam distillation setups are ideal for extracting oils from plants, as they gently capture aromatic compounds without degradation.
- Water Distillation: Equipment designed for water purification focuses on removing impurities, ensuring clean and safe water for consumption or laboratory use.
Production Capacity
Production capacity plays a crucial role in determining the type and size of distilling equipment you need. Choosing the right capacity ensures that your distillation process is efficient, cost-effective, and capable of meeting demand without excessive waste or operational strain. Below is a detailed breakdown of capacity options and their ideal applications:
1. Small-Scale Production
Small-scale equipment is designed for hobbyists, enthusiasts, or producers catering to niche markets. These setups are typically compact, affordable, and user-friendly, making them perfect for beginners or those working on a tight budget.
- Capacity:Ranges from 1 to 10 liters.
- Applications:Ideal for experimenting with small batches of spirits, essential oils, herbal distillates, or water purification.
Advantages:
- Requires minimal space, allowing for easy setup in home environments.
- Lower initial investment, making it accessible to newcomers.
- Allows for greater control and customization of recipes.
Challenges:
- Limited output, which may not meet growing demand if you scale up.
- Frequent cleaning and refilling may be required for continuous operation.
For instance, a 5-liter pot still is sufficient for a hobbyist producing small batches of ginor whiskey, ensuring the process remains manageable and enjoyable without overwhelming space or resources.
2. Medium-Scale Production
Medium-scale distilling equipment caters to craft distilleries or small businesses focusing on artisanal products. These setups strike a balance between manageable size and sufficient output, making them highly versatile.
- Capacity:Typically ranges from 50 to 500 liters.
- Applications:Perfect for boutique distilleries producing specialty spirits, such as single malt whiskey, flavored vodkas, or small-batch rum.
Advantages:
- Increased production volume to cater to local markets or small-scale commercial distribution.
- Often equipped with features like automated controls, allowing for consistency and ease of use.
- Supports experimentation with larger batches while maintaining artisanal quality.
Challenges:
- Higher initial investment compared to small-scale equipment.
- Requires dedicated space and compliance with commercial distilling regulations.
For example, a 200-liter hybrid still can enable a craft distiller to produce consistent high-quality vodka while retaining the flexibility to create limited-edition flavored batches.
3. Large-Scale Production
Large-scale equipment is essential for industrial distilleries or companies producing high volumes of distilled products. These systems are designed for efficiency, scalability, and compliance with stringent industrial standards.
- Capacity: Typically exceeds 1,000 liters. Some systems are capable of processing several thousand liters per batch.
- Applications:Suited for mass production of spirits, industrial-grade alcohol, or large-scale water purification.
Advantages:
- Handles large volumes efficiently, reducing operational downtime.
- Often integrated with advanced automation, ensuring consistent output and minimal manual intervention.
- Built for scalability, making it possible to expand production capacity with minimal additional investment.
Challenges:
- High initial cost, both for the equipment and the infrastructure needed to support it.
- Requires significant space and adherence to strict safety and regulatory standards.
- Maintenance and repairs can be complex and costly.
For instance, a 2,500-liter column still is suitable for a commercial distilleryproducing large quantities of neutral spirit for vodka or industrial alcohol used in pharmaceuticals and cleaning products.
Matching Capacity To Your Needs
When selecting the appropriate capacity, consider the following:
- Current Demand:Assess your current production goals. A small-scale setup may suffice for personal use, while commercial ventures will require medium or large-scale systems.
- Growth Potential:Plan for future expansion. If you anticipate increased demand, opt for scalable equipment that allows for upgrades.
- Budget:Balance capacity with affordability. While it may be tempting to invest in the largest system, smaller setups often offer better ROI for hobbyists or startups.
- Space Availability:Ensure your chosen equipment fits within your allocated space without compromising safety or efficiency.
What To Look Out For When Choosing Distilling Equipment
1. Material Quality And Durability
The material of your distilling equipment significantly affects both the quality of the product and the longevity of the equipment. Two primary materials dominate the market:
- Copper: Copper stills are renowned for their remarkable heat conductivity and capacity to eliminate sulfuric acid during the distillation process, resulting in higher-quality spirits with improved flavor. To keep it effective, copper must be cleaned frequently because it is subject to rusting.
- Stainless Steel: Stainless steel is easier to clean, corrosion-resistant, and more cost-effective than copper. It's a great option for large-scale enterprises like water distillation. For the best of all worlds, many distillers choose hybrid stills that combine the two materials, even though it doesn't improve flavor like copper does.
Types Of Distilling Equipment
1. Pot Stills
Pot stills are one of the oldest and most traditional forms of distillation equipment, recognized for their simplicity and ability to craft spirits with rich, complex flavors. Their design and operation are straightforward, making them an excellent option for smaller-scale operations or producers seeking a high degree of flavor retention.
How Pot Stills Works
Pot stills operate on a batch distillation principle. The wash or mash is poured into a large pot-shaped container made of copper or stainless steel. This container is heated, usually with direct flame or steam, causing the liquid to boil. The alcohol vapor, being lighter than water vapor, rises through a neck or lyne arm and passes into a condenser where it is cooled and returned to liquid form. This distilled liquid is collected, and depending on the desired purity and flavor profile, the process may be repeated multiple times.
Applications:
Pot stills excel at producing spirits that require bold and complex flavors, such as:
- Whiskey:Scotch and other single-malt varieties, where the robust grain flavors need to shine.
- Rum:Especially dark or spiced varieties, where the character of molasses or sugarcane is preserved.
- Brandy:Capturing the essence of fruits, particularly in small-batch productions.
Advantages:
- Flavor Enhancement:The flavor and character of the spirit are enhanced by the way pot stills are designed to retain contaminants and congeners in the finished product.
- Simplicity:They are easy to operate, requiring basic training and equipment knowledge.
- Versatility:Small adjustments in the process can create significantly different flavor profiles, ideal for artisanal producers.
Challenges:
- Limited Efficiency:Pot stills require multiple distillation runs to achieve higher alcohol content, which can be time-consuming.
- Batch Process: Unlike column stills, they cannot operate continuously, limiting output in large-scale operations.
For instance, a distiller aiming to produce a small-batch craft whiskey might choose a 500-liter pot still made of copper to enhance flavor by removing sulfur compounds during distillation.
2. Column Stills
Column stills, also known as continuous stills or reflux stills, are the pinnacle of efficiency in distillation equipment. They are designed for large-scale operations where consistency, high-purity alcohol, and speed are essential.
How Column Stills Works
Column stills consist of a tall, vertical structure divided into multiple sections or plates. Each plate acts as a mini-distillation unit, allowing the rising alcohol vapor to condense and re-vaporize multiple times as it moves up the column.
This repeated process ensures that the final product is highly pure, with minimal impurities. Heat is supplied at the base, while the liquid feed is introduced higher up the column. The alcohol vapor is collected at specific points along the column, depending on the desired purity level.
Applications:
Column stills are commonly used in:
- Vodka Production:High-purity alcohol is essential for creating neutral spirits.
- Industrial Alcohol:Used in pharmaceuticals or fuel-grade ethanol, where purity is non-negotiable.
- Large-Scale Rum or Whiskey:Certain mass-produced spirits benefit from the efficiency and consistency of column stills.
Advantages:
- Continuous Operation:Unlike pot stills, column stills can operate non-stop, making them ideal for large-scale production.
- High Alcohol Purity:Achieves purities of 95% or higher in a single run, essential for neutral spirits.
- Energy Efficiency:Requires less energy per unit of alcohol produced compared to batch distillation.
Challenges:
- Flavor Reduction:The focus on purity often removes congeners, leading to a less complex flavor profile.
- Cost: Initial investment and maintenance can be significantly higher than pot stills.
- Size and Space:Column stills are typically large and require ample space for installation.
For example, a vodka producer aiming for consistent, high-quality output would benefit from a 20-plate stainless steel column still, ensuring precise control over alcohol purity.
3. Hybrid Stills
Hybrid stills offer the best of both worlds, combining the flavor-enhancing characteristics of pot stills with the efficiency and purity of column stills. They are a favorite among craft distillers seeking versatility in their product lines.
How Hybrid Stills Works
A hybrid still typically includes a pot still base and a detachable column. The user can distill as they would with a traditional pot still for flavor-rich products or engage the column for high-purity distillation. Some designs allow the use of partial columns or selective reflux settings, providing unparalleled control over the distillation process.
Applications:
Hybrid stills are suitable for:
- Craft Distilleries:Producing a wide variety of spirits such as whiskey, gin, rum, and vodka.
- Experimentation:Ideal for distillers who want to refine their techniques or create unique blends.
Advantages:
- Versatility:Easily switch between batch distillation for complex flavors and continuous distillation for purity.
- Customization:Allows precise control over reflux, enabling tailored flavor and alcohol profiles.
- Space-Saving:Combines the functionality of two separate stills into one unit, reducing the need for additional equipment.
Challenges:
- Cost:Often more expensive than standalone pot or column stills due to added functionality.
- Learning Curve:Requires more skill and experience to fully utilize all features effectively.
For example, a craft distillery producing both single-malt whiskey and botanical gin might choose a hybrid still with a 1,000-liter pot and a detachable 8-plate column to accommodate diverse production needs.
Click the video below to gain more knowledge you would need to make an informed choice and elevate your distilling journey.
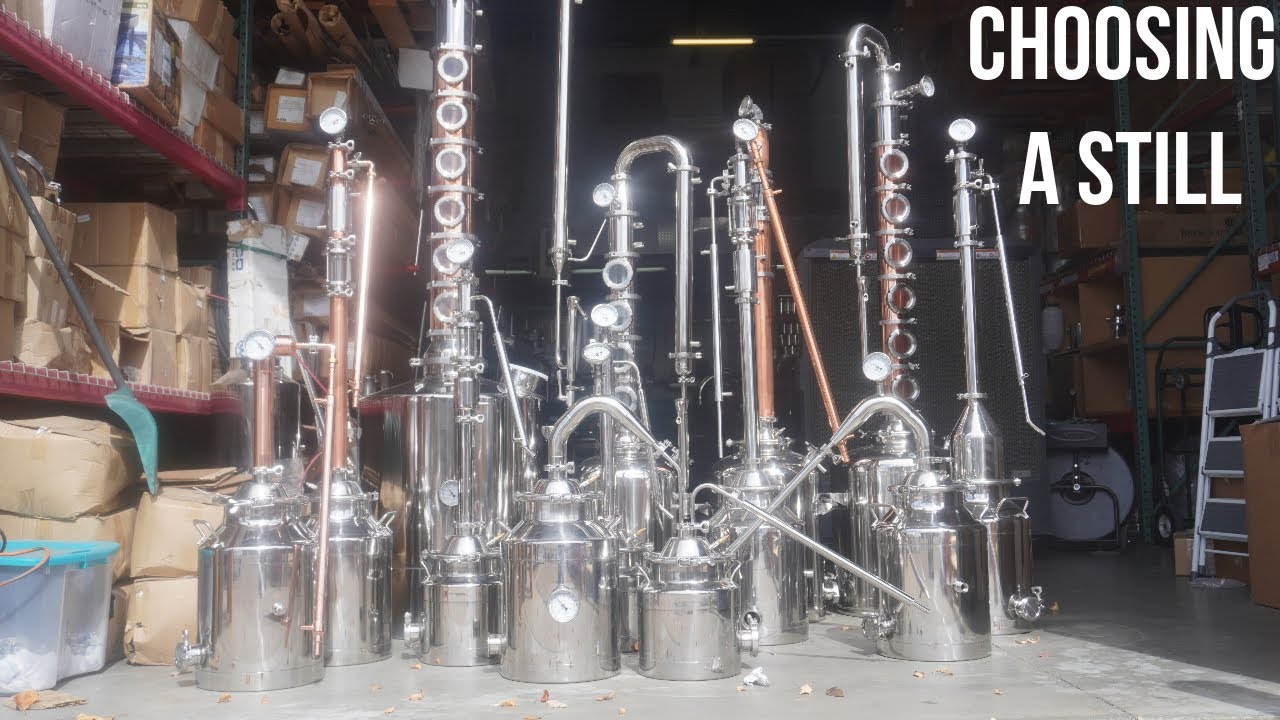
How to Choose The Right Still For You
Capacity And Scalability
When selecting distillation equipment, capacity and scalability are two of the most critical factors to consider. The capacity of your still dictates how much product you can produce in a single cycle, while scalability ensures that your operation can adapt to future growth. It’s essential to evaluate your immediate production needs and forecast potential expansion to make an informed investment.
Understanding Capacity
Capacity refers to the volume of liquid that the still can process in one distillation cycle. This is typically measured in liters or gallons and directly correlates with the size of your operation and production goals.
- Small-Scale Capacity (1–50 liters): Ideal for hobbyists or small-batch producers, small-capacity stills allow experimentation and the creation of unique, high-quality products without significant financial or space investments. However, such equipment can quickly become limiting if demand increases, requiring multiple cycles to meet production needs.
- Medium-Scale Capacity (50–500 liters): Suitable for craft distilleries aiming to balance small-batch quality with moderate production volume. Medium-sized stills provide flexibility, allowing for consistent output without the need for continuous operation.
- Large-Scale Capacity (1,000+ liters): Designed for industrial operations, these stills can handle significant volumes of liquid, making them indispensable for high-demand production. They ensure efficiency and consistency at scale, often incorporating advanced automation and monitoring features to maintain quality during mass production.
Planning For Scalability
While addressing your current production needs is essential, preparing for future scalability ensures long-term operational efficiency and reduces the likelihood of needing frequent upgrades. Here’s how to approach scalability:
- Anticipate Growth: Even if you’re starting small, consider how your market and demand might evolve. Upgrading equipment can be costly and time-consuming, so investing in a slightly larger or modular still can save money in the long run.
- Modular Equipment: Many manufacturers offer modular still designs that can grow with your operation. For instance, starting with a pot still and adding a column or extra plates as production scales up allows gradual investment aligned with growth.
- Consider Automation: Scalable equipment often includes automation features like temperature control, pressure regulation, and remote monitoring. These features reduce manual intervention, enabling consistent output even as production volumes increase.
- Space and Infrastructure: Ensure your facility can accommodate future upgrades. Larger stills require more space, enhanced ventilation, and stronger utility connections (e.g., water, electricity, or steam). Planning your layout with these factors in mind can prevent costly renovations down the line.
Balancing Current Needs And Future Goals
- For Small Producers: If you’re a hobbyist or niche producer, start with a smaller still but choose one with scalability options, such as additional plates or attachable columns.
- For Medium Producers: Investing in mid-range capacity stills with modular capabilities ensures you can cater to increasing demand without compromising product quality.
- For Large Producers: Large-scale operations should prioritize high-capacity equipment with automation to meet high demand efficiently while maintaining consistency.
Safety Considerations In Distilling
Distilling involves working with high temperatures, flammable materials, and pressurized systems, which can create potentially dangerous situations if safety measures are not prioritized. Ensuring your equipment has built-in safety features is critical for protecting both operators and facilities. Below are key safety features to look for and why they matter.
1. Pressure Relief Valves
Pressure relief valves are essential components that protect against excessive pressure buildup in your distillation system. During the distillation process, liquids are heated, and pressure can increase rapidly inside the equipment.
- Why They Matter: Without a functioning pressure relief valve, pressure buildup can lead to equipment damage or even explosions. This feature automatically releases excess pressure, maintaining safe operating conditions.
- Tips for Selection: Choose equipment with high-quality, adjustable pressure relief valves designed for the specific operating pressure of your setup. Regularly inspect and test these valves to ensure they function correctly.
2. Thermal Insulation
Distillation equipment operates at extremely high temperatures, which can pose a risk of burns to operators if surfaces are left exposed. Thermal insulation is designed to minimize the risk of accidental contact with hot surfaces.
- Why It’s Important: Proper insulation not only protects users from burns but also improves energy efficiency by retaining heat within the system. This ensures the distillation process runs smoothly without unnecessary heat loss.
- Key Features to Look For: Opt for equipment with insulated columns, boilers, and piping. Materials like fiberglass, ceramic, or specialized foam are commonly used for insulation in distillation setups.
3. Leak-Proof Seals
Leak-proof seals are critical for preventing the escape of vapors and liquids during distillation. Vapors, especially from alcohol and other flammable substances, can pose serious fire and health hazards if they leak into the surrounding environment.
- Why It’s Crucial: Leaking vapors reduce efficiency, waste valuable product, and can create a fire hazard in areas with open flames or electrical equipment. Proper seals also help maintain consistent pressure and temperature, which is vital for producing high-quality distillates.
- What to Look For: Ensure all connections, joints, and gaskets in the equipment are made from durable, heat-resistant materials such as silicone or PTFE (Teflon). Periodically check and replace seals to prevent wear and tear over time.
Additional Safety Tips For Distilling
- Proper Ventilation: Ensure your workspace has adequate ventilation to disperse any vapors that may escape. A well-ventilated environment reduces the risk of fire and exposure to harmful fumes.
- Fire Safety Equipment: Keep fire extinguishers rated for chemical and electrical fires nearby, as well as fire blankets for emergencies.
- Monitoring Systems: Advanced equipment may include temperature and pressure monitors, allowing you to closely track the process and react quickly to abnormalities.
- Training and Precautions: Anyone operating the distillation equipment should be trained in its use and aware of emergency protocols. Always follow the manufacturer’s safety guidelines and instructions.
Why Safety Is Non-Negotiable
In distillation, neglecting safety precautions can have severe consequences, ranging from minor injuries to catastrophic accidents. By choosing equipment with essential safety features and maintaining diligent operational practices, you create a safer environment for your team and ensure the longevity of your equipment. Safety is not just a consideration, it’s a commitment to responsible distillation.
Ease Of Use And Maintenance
When choosing distilling equipment, it’s important to consider how easy it is to operate and maintain. Complicated equipment can lead to errors, delays, and frustration, especially for those new to distillation. User-friendly designs and well-thought-out maintenance features make the entire process more efficient and enjoyable. Here’s a detailed look at what to consider:
User-Friendly Design
A well-designed piece of equipment should simplify the distillation process, not complicate it. User-friendly equipment allows you to focus on the craft of distilling rather than struggling with technical issues.
- Straightforward Operation: Look for equipment with clear labels, intuitive controls, and easy-to-follow instructions. This is especially important for beginners who might not be familiar with complex setups.
- Automated Features: Many modern distilling systems include automation, such as programmable temperature settings, timers, and pressure controls. These features minimize the need for constant monitoring and reduce the risk of mistakes.
- Ergonomic Layout: Equipment designed with ergonomics in mind ensures that handles, valves, and controls are positioned for easy access, making operation smoother and reducing physical strain.
Maintenance Features
Proper maintenance is essential to keep your distilling equipment working efficiently and producing high-quality results. Equipment with maintenance-friendly features saves time and effort in the long run.
- Easy-to-Clean Parts: Cleaning is a crucial step after each distillation cycle. Choose equipment with detachable or modular parts that are easy to disassemble and clean. Features like wide openings and smooth interiors can simplify the cleaning process.
- Accessible Cleaning Ports: Some distilling systems come with dedicated cleaning ports or access panels that allow you to reach hard-to-clean areas. This ensures thorough cleaning, which is vital for preventing contamination and maintaining product quality.
- Durable Materials: High-quality materials like stainless steel are not only durable but also easier to clean and maintain compared to cheaper alternatives. Look for materials that resist rust, staining, and wear over time.
Minimizing Maintenance Downtime
Equipment that requires frequent or complicated maintenance can disrupt your distilling schedule. Opt for systems designed to minimize downtime.
- Replaceable Parts: Check if the equipment allows for easy replacement of wear-and-tear components, like seals or gaskets. This saves you from having to replace the entire system due to minor issues.
- Diagnostic Tools: Some advanced systems include diagnostic indicators or alerts for maintenance needs, such as cleaning or part replacement. These features help you stay proactive about upkeep.
Benefits Of Choosing Easy-to-Use And Maintain Equipment
- Reduced Errors: Simpler setups mean fewer chances of operational mistakes, leading to better results.
- Time-Saving: Equipment that is easy to operate and maintain allows you to focus more on distilling and less on troubleshooting or cleaning.
- Longer Lifespan: Regular maintenance is easier to manage with user-friendly features, ensuring your equipment lasts longer and performs consistently.
- Cost-Effective: Properly maintained equipment reduces the need for costly repairs or replacements over time.
Key Takeaway
Distilling equipment should make your work easier, not harder. By choosing systems with user-friendly designs and practical maintenance features, you can focus on producing high-quality spirits while ensuring your equipment remains in top condition for years to come. Investing in ease of use and maintenance isn’t just a convenience, it’s a smart decision for efficiency, safety, and long-term success. If you’re determined to become a master distiller, these features will help you perfect your craft while avoiding unnecessary setbacks.
Energy Efficiency
Energy efficiency is a key factor to consider when choosing distilling equipment, as it directly impacts your operating costs and environmental footprint. Equipment that uses energy wisely can save you significant money over time while also contributing to sustainability efforts.
Look for systems designed to minimize waste, such as insulated boilers. These boilers retain heat effectively, reducing the amount of energy needed to maintain the right temperatures. Additionally, modern distilling equipment often comes with features like energy-efficient burners, heat exchangers, or smart controls that optimize power usage without compromising performance.
Cost Vs. Value
Choosing the right distilling equipment involves more than just looking at the price tag. While low-cost options may seem appealing, they often come with downsides like poor quality, frequent breakdowns, or limited efficiency. High-quality equipment might require a larger initial investment, but it provides lasting value.
Durable materials like stainless steel and well-built designs ensure the equipment performs reliably for years. High-end systems also often include safety features, energy-saving designs, and advanced controls that improve both production quality and ease of use. These factors make them a better choice for long-term success.
It's also important to think about the overall cost of owning and operating the equipment. Beyond the purchase price, consider how much you’ll spend on maintenance, energy, and repairs. For instance, energy-efficient equipment may cost more upfront but can save a significant amount in electricity or fuel bills over time.
Brand Reputation And Support
Choosing a distilling equipment brand with a strong reputation is essential for a reliable and hassle-free experience. Reputable brands have a proven track record of delivering high-quality products that stand the test of time. Look for manufacturers known for their craftsmanship, innovative designs, and commitment to safety standards.
Positive customer reviews and testimonials can provide valuable insights into the equipment's performance and the company's reliability. A well-regarded brand often offers warranties, demonstrating confidence in its products and giving you peace of mind about your investment. If you’re also looking to improve your skills in other areas, learning how to complete missions efficiently in lost lifecould provide useful strategies to boost your efficiency in the game.
Common Mistakes To Avoid
1. Overlooking Regulations
Local laws govern distilling, especially for alcohol production. Failure to comply can result in fines or equipment confiscation. Always verify the legality of your distillation plans before investing.
2. Focusing Solely On Price
Cheap equipment may seem appealing but often sacrifices quality, safety, or durability. Striking a balance between cost and quality ensures better long-term results.
3. Underestimating Production Needs
Buying equipment with insufficient capacity can lead to inefficiencies, while overestimating can result in unnecessary expenses. Evaluate your production needs carefully and consider future growth.
FAQs
What Makes You A Master Distiller?
Ultimately, Master distillers, whether in beer, whiskey, gin, or juice, need to know how to make great products, but they also need to understand their industry inside and out. They have to understand things such as weather, geography, chemistry and more, and how it affects the work they do.
What Are The 4 Pieces Of Equipment Required For The Process Of Distillation?
There are three essential pieces of distillation equipment needed to carry out the process;
- Reboiler or Pot - Used to heat the source liquid.
- Condenser - The heated vapour is cooled back to a liquid state.
- Receiver Flask - The device into which the concentrate/distillate is collected.
What Is The Setup For Simple Distillation?
Simple Distillation SetupThe apparatus involves the following important components: A heat source, which raises the mixture to the appropriate temperature. A round-bottom boiling flask, which contains your liquid mixture or “analyte”. A sand bath, which ensures even heating of your boiling flask.
Are There Legal Requirements For Distilling At Home?
Yes, local laws vary. In many places, home distillation of alcohol is restricted or requires a permit. Always check regulations before purchasing equipment.
What’s The Best Equipment For Beginners?
Pot stills are user-friendly and effective for beginners. They’re ideal for crafting spirits in small batches.
Final Thoughts
Choosing the right distilling equipment isn’t just buying a tool, it’s an investment in your craft and future success. By knowing your goals, considering important factors, and avoiding common mistakes, you can find equipment that fits your needs.
Hobbyists and commercial distillers alike can achieve great results with the right gear, bringing confidence and ease to every batch.